顯微組織:樣品未見過燒,平均晶粒直徑約為91.6μm,相當(dāng)GB/T 3246.1-2012的4級,如圖5:
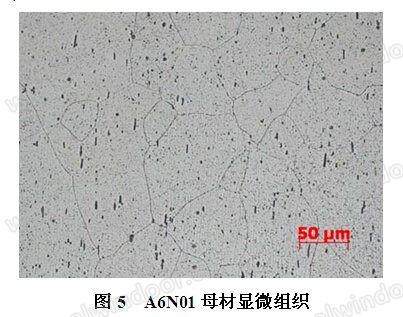
(2)A7N01型材樣品金相試驗結(jié)果
低倍組織:樣品檢測面上未見粗晶環(huán),未見裂紋、縮尾、光亮晶粒、非金屬夾雜、外來金屬夾雜、白斑及化合物等點狀缺陷,低倍晶粒度相當(dāng)于GB/T 3246.2-2012的一級。
顯微組織:樣品未見過燒,平均晶粒度約為3.3μm,相當(dāng)于GB/T 3246.1-2012的13.5級,如圖6所示。
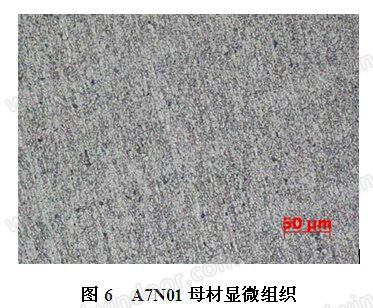
3.5其它試驗結(jié)果
試樣進(jìn)行的其它試驗結(jié)果如表7所示:
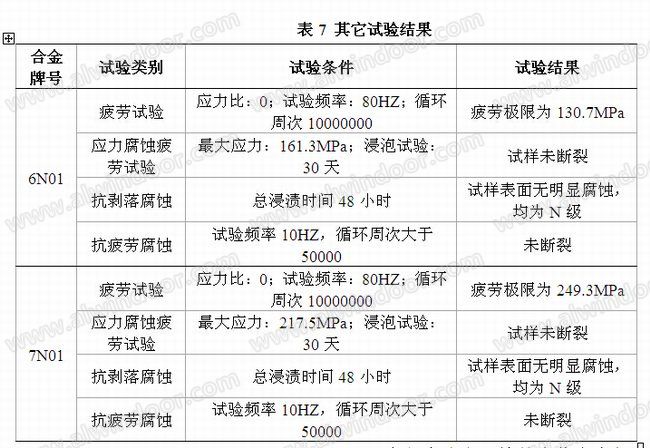
型材焊接后還需進(jìn)行焊縫基本性能、熱裂紋、疲勞強度及焊縫應(yīng)力腐蝕等相關(guān)試驗,檢測的焊接性能均應(yīng)滿足列車型材焊接性能要求。試驗按和諧號CRH6列車車體標(biāo)準(zhǔn)焊接了12米長車體,各款型材拼接良好,車體累計公差小于10mm,焊接后的車體效果如圖7所示。

由列車型材產(chǎn)品的檢測結(jié)果可知,所有檢測結(jié)果均滿足列車型材標(biāo)準(zhǔn)要求。因此,試驗采用的工藝技術(shù)參數(shù)是完全可行的。
3.6試驗工藝討論
3.6.1熔鑄工藝討論
在熔鑄生產(chǎn)過程中,對于A6N01鑄棒的生產(chǎn)要點與其它6系合金較為相似,在此不做敘述。而在進(jìn)行A7N01合金熔煉鑄造過程時,因為其合金化程度比較高,在熔鑄過程中需控制的參數(shù)比較嚴(yán),試驗生產(chǎn)過程需注意以下方面:
(1)鋅密度大,加入鋁熔體中易沉爐底不易熔化,鋅直接與火焰接觸易氧化燒損,加入方式較
大程度決定了鋅的實收率高低,通過生產(chǎn)試制驗
證,當(dāng)爐料熔化有一層液體金屬再均勻加入鋅錠的方式可行,燒損少;
(2)在Al―Zn―Mg系合金中微量鈦能細(xì)化合金在鑄態(tài)時的晶粒,避免鑄錠出現(xiàn)羽毛狀晶,降低裂紋趨向性,鈦含量應(yīng)控制在0.02~0.06%之間;
(3)通入的高純Ar氣必須99.99%以上,精煉時間不低于20分鐘,在鑄造前務(wù)必將溜槽及鑄造盤清掃加溫烘干,避免將氫帶入鋁合金熔體。
3.6.2模具設(shè)計討論
合理的模具設(shè)計是實現(xiàn)列車型材產(chǎn)品成型和尺寸精度的重要保證,也是獲得產(chǎn)品優(yōu)良性能的關(guān)鍵點,尤其在控制空心鋁型材的焊縫組織和型材力學(xué)性能方面尤為重要。模具分流孔的大小、數(shù)量、形狀、分布位置,焊合室的形狀和尺寸,模芯的結(jié)構(gòu)等技術(shù)參數(shù)是在設(shè)計模具時所需考慮的重要部分。經(jīng)過多次試驗研究,模具設(shè)計時需注意如下幾點:
(1)分流孔設(shè)計:對于空腔且壁厚較薄的型材,設(shè)計靠兩邊的分流孔應(yīng)比中心分流孔大,可彌補靠邊金屬流動壓力小,供料困難的不足;
(2)分流橋設(shè)計:為了降低焊合條紋出現(xiàn)的機會或減輕焊合條紋的程度,減少分流橋下死區(qū),把分流橋的倒角設(shè)計成水滴形,并把分流橋橋尖設(shè)計成20°錐形;
(3)焊合室的設(shè)計:針對多型腔大截面型材的模具設(shè)計,焊合室高度宜大于45mm,合理選擇50~55mm,增強靜壓力和焊合時間,使型材金屬性能達(dá)到強化效果。同時,焊合室周邊用R5圓角過渡,減少死區(qū),有利于金屬流動;
(4)工作帶的設(shè)計:凹模工作帶在設(shè)計時,把壁厚薄、被分流橋遮蓋住部分的筋部工作帶設(shè)計為最短。從降低擠壓力的角度出發(fā),在保證制品成型精度的情況下盡量短。
3.6.3擠壓及熱處理工藝討論
車體型材對綜合性能的要求非常嚴(yán)格,擠壓生產(chǎn)過程中要避免出現(xiàn)型材晶粒度及產(chǎn)品的伸長率達(dá)不到標(biāo)準(zhǔn)要求的現(xiàn)象。因此,我們在保證鑄棒及模具質(zhì)量的前提下,從擠壓工藝的控制以及型材時效制度等方面進(jìn)行了大量試驗。
(1)在型材時效工藝選擇時,對不同時效制度處理的型材測定其室溫力學(xué)性能(抗拉強度Rm、屈服強度RP0.2及伸長率A50mm),具體如表8、表9所示。
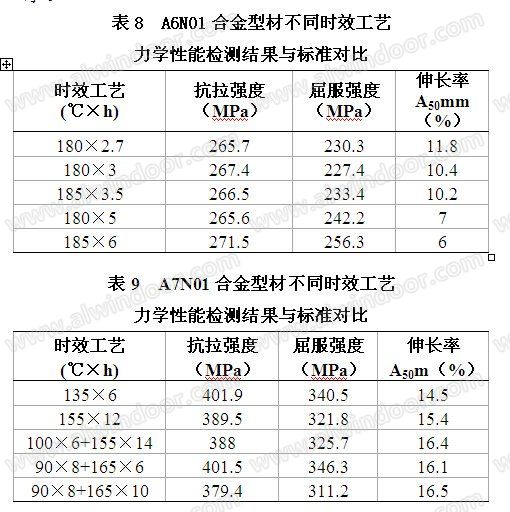
從試驗數(shù)據(jù)中,我們選取了A6N01為180℃×2.7h和A7N01為90℃×8h+165℃×10h的二級時效工藝,保證了時效后型材的力學(xué)性能滿足要求。
(2)A7N01鋁合金的合金化程度高,合金的抗應(yīng)力腐蝕開裂性能及均勻化較差,在擠壓過程中,通過對鑄錠的溫度,擠壓速度等進(jìn)行優(yōu)化,特別是減慢在線淬火速度,能有效地提高型材的抗應(yīng)力腐蝕開裂性能。
(3)為使擠壓型材整體性能均勻,生產(chǎn)采用等溫擠壓,要求擠壓前加熱的鑄棒從前到后沿軸線溫度逐漸降低,形成每米鑄棒20℃的溫度梯度。擠壓成型后,為獲得穩(wěn)定的組織性能,型材在冷床前12m采用強冷風(fēng)冷卻,12m后采用弱冷風(fēng)吹至型材完全冷卻。
(4)因型材長度為24.5m,試驗用時效爐為30m長,在時效過程中,對時效爐前后需校正好,溫差應(yīng)不大于2℃。時效時,應(yīng)將升溫時間調(diào)長,試驗采用的升溫時間為3個小時,有利于去除型材的內(nèi)應(yīng)力(詞條“內(nèi)應(yīng)力”由行業(yè)大百科提供)。
4、結(jié)論
(1)對A7N01合金型材自然時效后再進(jìn)行雙級時效,并且隨著時效時間的延長,不僅有效提高該合金的抗應(yīng)力腐蝕性能,而且在損失少許的力學(xué)性能下,可以大幅度提高合金的延伸率。對于A6N01合金型材,在固定的溫度狀態(tài)下,隨著時效時間的延長,可以有效提高該合金的抗應(yīng)力腐蝕性能和力學(xué)性能,但是合金型材的延伸率是下降的,所以我們選擇的是欠時效工藝。
(2)在模具設(shè)計過程中,需改變以成型率作為設(shè)計重點的思想,而需優(yōu)先考慮產(chǎn)品性能要求。模具焊合室不宜過深,一般以40~55mm為宜,且小芯頭的空刀位置加工需盡可能光滑,這樣生產(chǎn)出的型材晶粒度才更易達(dá)到一級的標(biāo)準(zhǔn)。
(3)企業(yè)如從建筑型材到生產(chǎn)大型復(fù)雜的列車車體用鋁材(詞條“鋁材”由行業(yè)大百科提供),除配套一些必備的硬件設(shè)備,如精密模具加工設(shè)備、大型擠壓設(shè)備、溫控精確的時效爐等,還需加強技術(shù)人才的儲備以及技術(shù)人員和生產(chǎn)員工的專業(yè)技能培訓(xùn),不斷摸索總結(jié)工藝并做到認(rèn)真嚴(yán)格執(zhí)行工藝技術(shù)要求。
(4)建立詳細(xì)的產(chǎn)品跟蹤檔案,從原材料采購、熔鑄、擠壓、檢驗檢測及包裝儲運各工序?qū)γ總產(chǎn)品都要有完整詳細(xì)的記錄,確保產(chǎn)品信息及可追溯性。
參考文獻(xiàn):
[1] 肖亞慶,謝水生,劉靜安等.鋁加工技術(shù)實用手冊[M].北京:冶金工業(yè)出版社,2005.
[2] 王祝堂,田榮璋.鋁合金及其加工手冊[M].長沙:中南大學(xué)出版社,1989.
上一頁12下一頁